Some Assembly Required
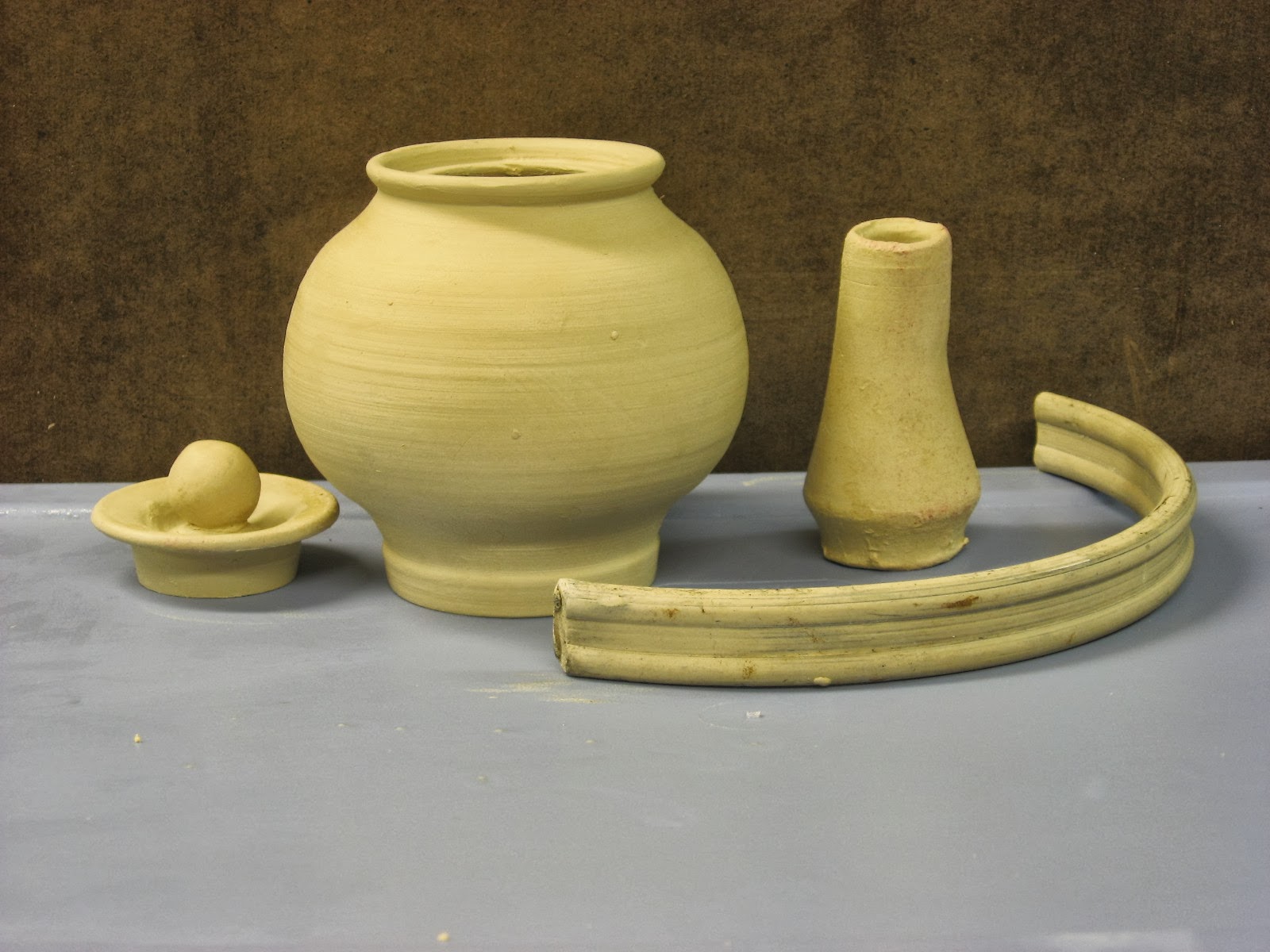
I create the separate pieces of a teapot at different times and allow them to dry to a leather hard state. When the clay is leather hard it can be handled without deforming the clay, but soft enough to manipulate and assemble the pieces. From left to right is the teapot lid, body and spout, along with an handle that has been extruded. The extruder's die was custom made by me. (Sorry for the yellow hue in the pictures. Either the camera flash malfunctioned or the fluorescent ceiling lights interfered with the flash.) I start with the spout. After imagining it on the teapot body, I cut the bottom of the spout to fit the curve of the body. Next I scratch an outline at the location of the spout on the body. Using my thumb I press the clay inward. This is the beginning of the internal strainer that is part of all of my teapots. Next I create the internal strainer by making small holes in the clay. Some use a set pattern for these holes. I don